プロジェクトストーリー
圧延銅箔 供給能力向上プロジェクト
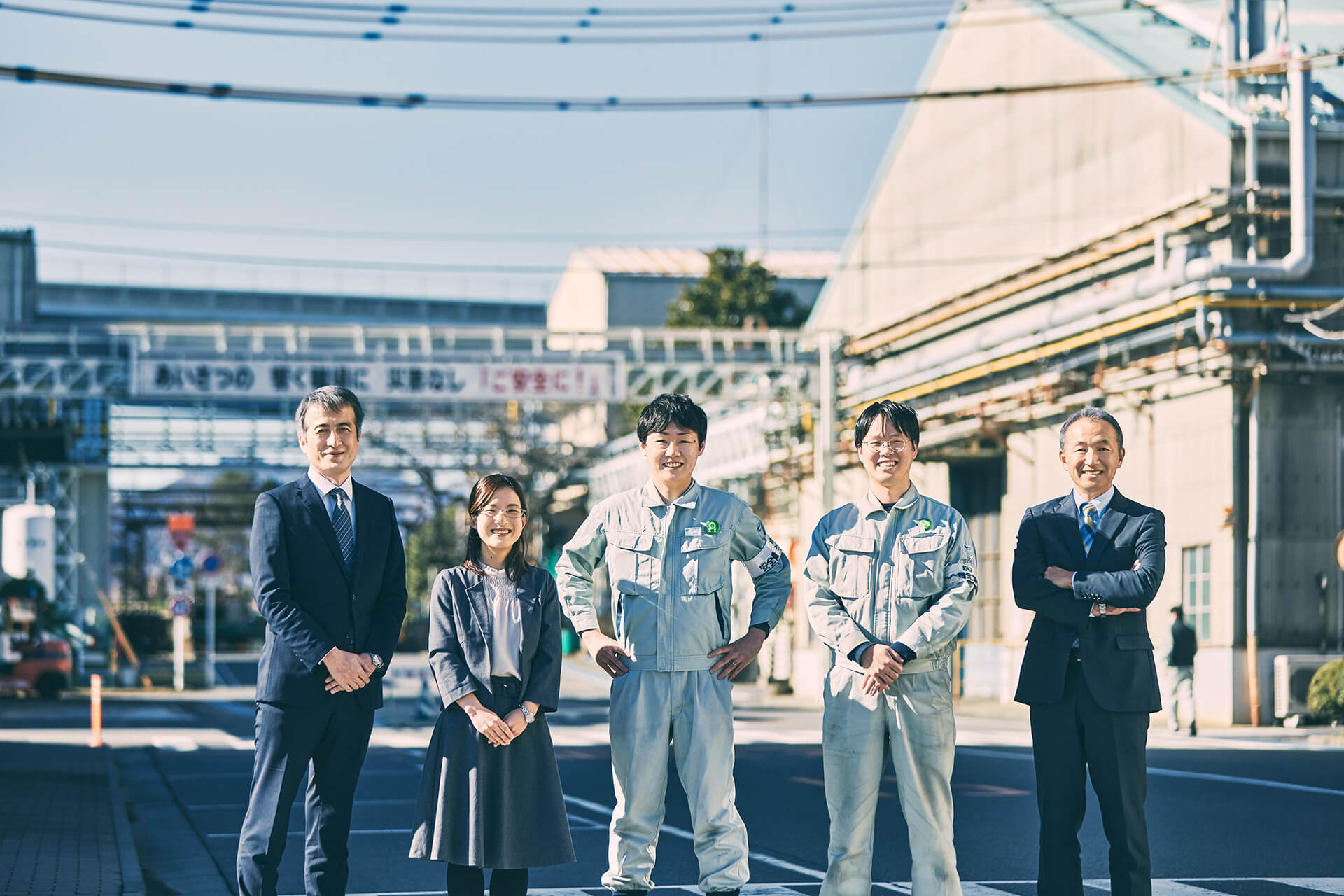
圧延銅箔──。スマートフォンなどの電子機器にとってなくてはならない素材であり、JX金属の主力製品の一つだ。「銅インゴット」と呼ばれる銅の厚板を、複数の圧延設備によってミクロン単位まで薄く延ばすことでつくられる。その薄さは用途によってさまざまだが、JX金属は独自の技術により0.005mm(=髪の毛の10分の1)という世界一薄い圧延銅箔をつくることができる。また、資源開発から圧延工程まで一貫して自社で行っているのは、世界を見てもJX金属だけだ。年々需要が高まり続け、現在では80%という世界トップのシェアを誇る。
事業拡大は順風満帆のように見えた。しかし2017年、急拡大した需要が供給能力を上回るという予測が算出される。供給はメーカーの存在意義。一刻も早く供給能力を上げなければ……。非鉄金属業界のリーディングカンパニーとしての威信をかけた大型プロジェクトが始まった。
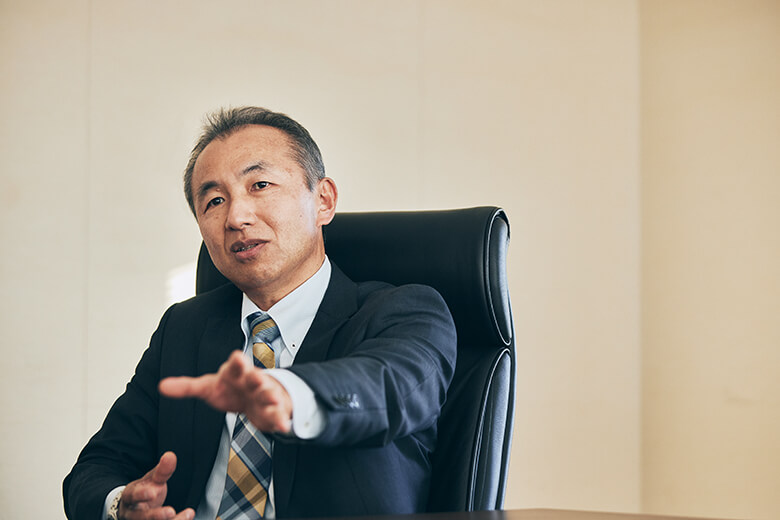
材料・プロセス
理工学研究科 金属工学専攻 修了
1991年 新卒入社
本社サポートチームの一員として、技術や市場動向を調査し、プロジェクト全体の進捗管理を行う。
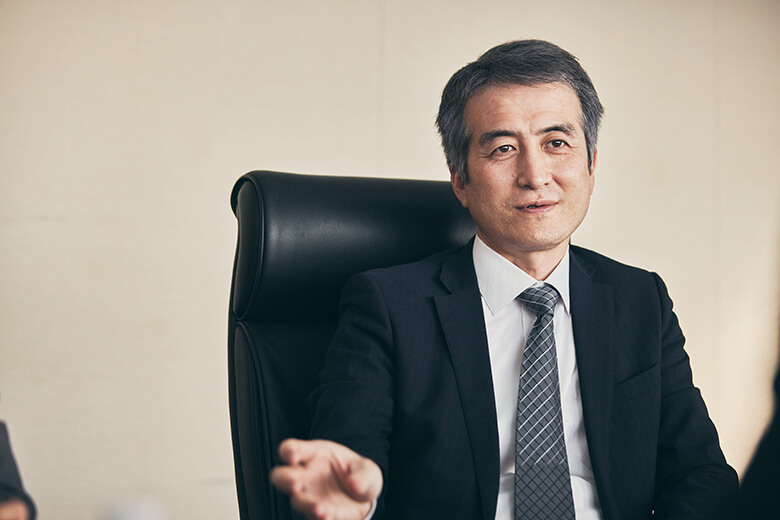
先端素材営業
経済学部 経営学科 卒
2014年 キャリア入社
営業担当として顧客へのヒアリングや供給に関する情報提供を行う。

材料・プロセス
理工学教育部 環境応用化学専攻 修了
2018年 キャリア入社
製造担当として、圧延銅箔製造時に用いる油を取り除くための脱脂設備導入を主導。
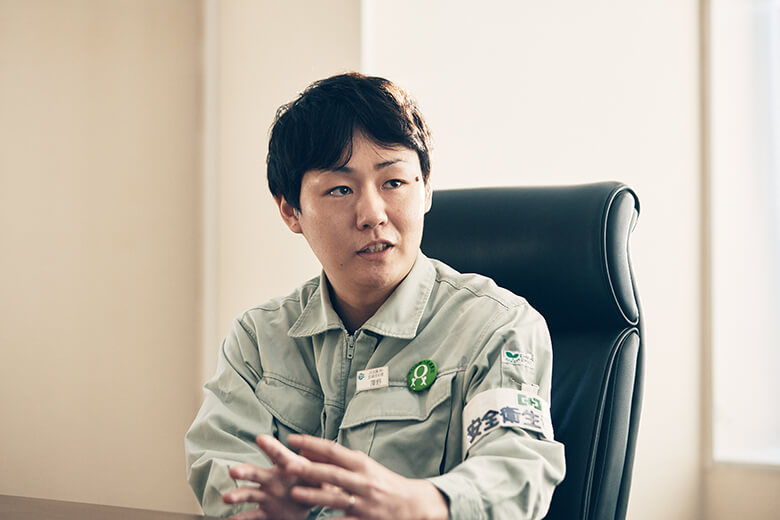
プラントエンジニア
工学府 物理情報工学専攻 修了
2016年 新卒入社
圧延設備の新規導入における、企画計画から設備立上げまでの一連のエンジニアリング業務を担当。
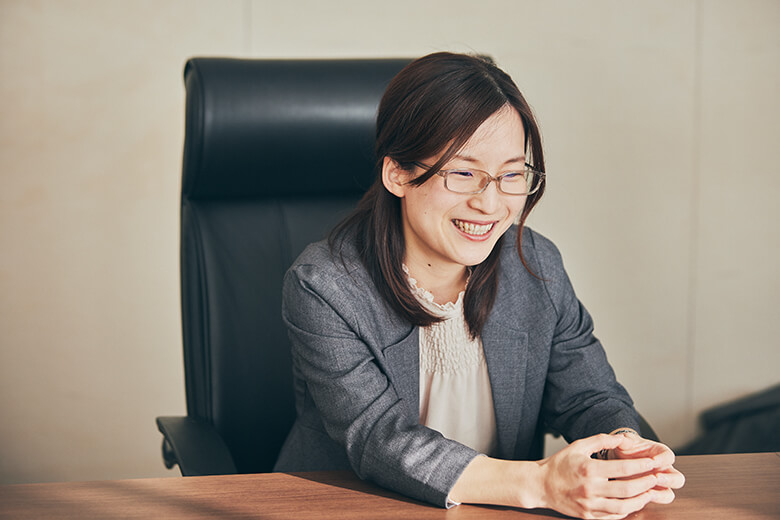
先端素材営業
社会学部 卒
2017年 新卒入社
圧延銅箔製造のリードタイム短縮を目指し、サプライチェーンの最適化を担当。
急拡大した圧延銅箔需要
チームで議論を重ね、
未来を予測する
JX金属でしかつくることのできない圧延銅箔を、安定的に市場へ供給する──。この絶対的な使命が揺らいでしまうほど、2017年の需要増は急激だった。

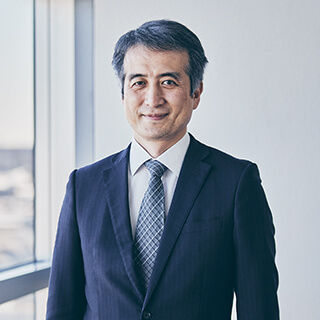
当社が2017〜2019年度中期経営計画の基本方針として掲げていたように、スマートフォンの高機能・多機能化による需要増などを見込んで、圧延銅箔の生産能力増強を行うことは事業戦略上の既定路線でした。しかし、予測をはるかに上回る急激な需要拡大のため、市場が求める生産量や技術動向について早急に洗い直す必要に迫られたのです。
圧延銅箔は最先端の電子材料に不可欠な素材だ。世の中の電子機器が増えるほど必要量は増加するし、求められる性能も変わる。例えば、昨今のスマートフォンの内蔵カメラは新機種が出るたびに搭載数が増えている。すると内部の回路基板は増え、そこに使われる圧延銅箔の需要も高まる。加えて高機能化が進むにつれ、高い折り曲げ性能や高強度、高い導電性能も求められるようになる。他にも、今後IoTやAIが進化し、自動運転など先端技術を活用したプロダクトが世の中に広がれば、圧延銅箔の需要が一層高まることは明白だった。
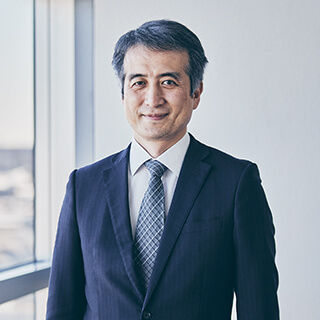
販売予測は、お客様へのヒアリングをもとに立てていきます。しかし、お客様としては必要なときに必要な量を必ず入手したいという思いが働き、保険をかける意味合いで数量を多めに伝える場合もあります。そこを見極めるためには圧延銅箔の用途といった補足情報が欠かせません。既存製品用なのか、新製品用なのか、さまざまなことをヒアリングします。また、電子材料は最終製品の需要に大きく左右されます。市場調査の実施や専門家へのヒアリングも大切です。そこで得られた情報に我々の経験則も交えながら、本当に必要な数量を営業チームで議論を重ねながら予測していきました。
最適な生産能力を導き出す
生産能力増強にあたって、販売予測と同様に技術動向の予測も重要だ。生産設備には仕様があり、つくることのできる製品スペックが決まっている。圧延銅箔は銅インゴットを薄く延ばしてつくられる。どこまで薄くできるかは設備の仕様次第だ。そのため将来顧客から求められるであろう製品スペックを予測し、ニーズに応えられる設備を導入しておく必要がある。

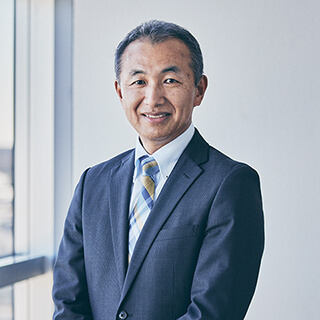
だからといって、不用意にオーバースペックの設備にすると、コストが膨らみ納期は延びてしまいます。それに圧延銅箔の製造は多少高いスペックを要求されても、設備改良と工程改善を組み合わせることによって対応することが可能です。そのため“現行と同等スペックの製品をつくれる設備を入れて、性能向上には改良で対応する”のか、“基本仕様から高スペックな製品をつくれる設備にする”のかを判断しなければなりませんでした。
いずれにしても、技術動向を予測できなければ答えは出せない。福嶋は顧客のもとへ足を運び、技術に関するニーズをかき集めた。そして電子機器のロードマップをもとに設備の仕様を見極めようとした。
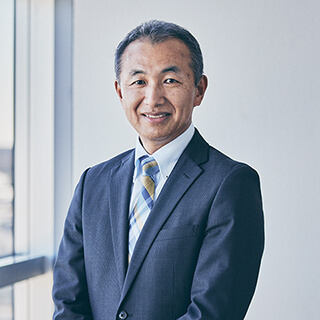
スマートフォンであれば、どのタイミングで4Gから5Gへ完全に切り替わり、そして6Gへ移行するのか、おおまかなロードマップはできています。自動運転も実用化が何年頃になりそうか分かれば、電子材料が必要となる時期を予測できるでしょう。そこに、例えば5Gで必要となる製品スペックがどの程度なのかという情報を加味することで、設備の仕様を予測することが可能になります。
営業、市場開発、設備を新設する工場の工場長なども加わり、生産量や設備仕様、投資額といった検討を重ねながら内容を詰めていった。そして2017年12月、プロジェクトの決裁を得るべく役員会に臨んだ。
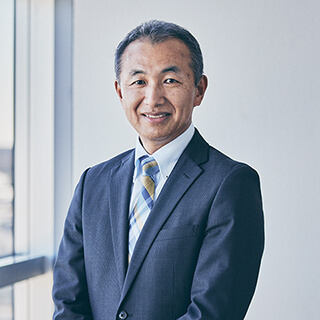
「生産能力を2017年比で30%増強する」「現行製品をつくれる設備を導入して、性能向上には改良で対応する」──。プロジェクトチームで導き出した結論に対して、経営層からはシビアな指摘が次々と飛んできました。その一つひとつに答えて妥当性を納得してもらえなければ、プロジェクトは前に進みません。必死でしたね。
やがて無事に決裁は得られた。福嶋は自分が発した言葉の重みを噛みしめ、その責任を背負う覚悟を固めながら役員会を後にした。そしてプロジェクトのメインステージは、神奈川県の倉見工場へと移っていく。
工場のプライドをかけて
「小さな気づき」
2018年、京堂は圧延銅箔の生産能力向上プロジェクトにおける、脱脂ラインの主担当となった。前職は異業界だったため、圧延銅箔の製造に関する知識は乏しい。それに彼は当時キャリア入社したばかり。にもかかわらず重要なポジションを任されたのだった。

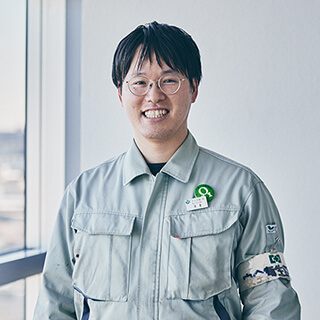
こんな大規模プロジェクトに、入社早々携わることになるなんて正直驚きました。圧延銅箔はJX金属の主力製品。プレッシャーも大きかったです。でも、それ以上にワクワクしている自分がいました。
銅インゴットを圧延する際、専用の油を使用する。しかし、そのままでは製品として販売できない。脱脂ラインは、圧延銅箔表面の油を取り除く役割を担う。プロジェクトスタート時、既存の脱脂ラインにおいて二つの課題が顕在化していた。一つは設備を速く稼働させると銅箔にシワができること。もう一つは圧延銅箔全長の表面検査ができないまま、製品の表面処理を行う日立事業所へ送られ、そこで圧延銅箔の一部に不良が検出されることだ。
シワについては脱脂槽の機構を変更することで解決できた。しかし、脱脂後に用いる表面検査機の選定でてこずることになる。既存の表面検査機では3種類の品質不良が確認されていた。新しく設置するものも、それらすべてを検知できるものでなければならない。発注先の設備メーカーを3社まで絞り込み、カットした圧延銅箔のサンプルを渡し、3種類の不良を検知できるか試してもらった。3社とも「できる」と回答してきた。従来であれば、この時点で価格などを鑑みて発注先を決める。しかし、彼は「もう一歩踏み込む必要性」を感じていた。
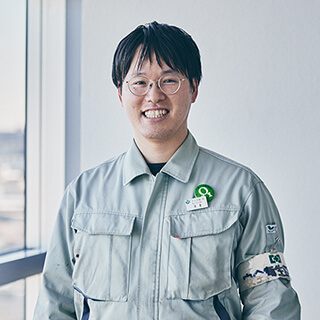
脱脂ラインが稼働しているときは銅箔に張力がかかっています。つまりサンプルとは検査条件が異なるということ。脱脂ラインが稼働している状況をデモ機で再現するべきだと主張しました。
デモを行うためには、稼働しているラインを一時的に停止しなければならない。ところが、当時生産ラインはフル稼働しており、デモのために一部を止められるような状況ではなかった。彼は上長に相談して圧延銅箔とは別のラインを1週間だけ借りてデモを行った。
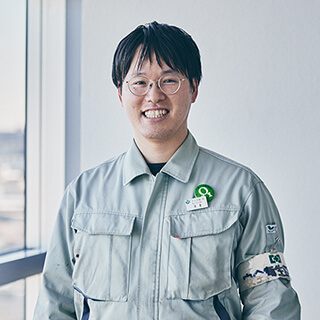
脱脂ラインを再現すると、課題がいくつも出てきました。取り付けるスプールがまるで違う。それに張力も低い。同じ条件を整えるため、銅箔の幅を変えて張力を上げるなど試行錯誤しました。また設備の仕様上、できないこと、してはいけないこともあります。現場の人たちや別ラインの製造担当者と密にコミュニケーションを取りながら、一つひとつ課題をクリアしていきました。
デモの結果、3社のうち1社の検査機は要件を満たさなかった。要件を満たした2社でさらに検討を行い、発注先は決定された。京堂の感じた“もう一歩踏み込む必要性”。それはほんの些細な気づきだった。しかしその気づきがなければ、数千万円という投資を無駄にしてしまう可能性があった。
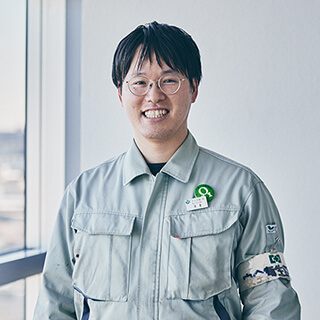
ほっとしましたね。上長や別ラインの担当者など、多くの人に骨を折らせることになってしまいましたが、サンプル調査だけでやめなくて本当によかったです。それに、入社間もないタイミングで現場の人たちの声を直接聞ける機会を持てたことが、これからの自分のキャリアに生きてくると感じています。
1カ月の遅れを取り戻せ
京堂が脱脂ラインの導入に奮闘していた頃、圧延設備導入のミッションを担っていた澤野は焦燥感にさいなまれていた。
プロジェクトにアサインされた当時、彼は入社3年目だった。倉見工場で行われたキックオフミーティングに参加した際、正面にズラリと並んだ錚々たるメンバーに、会社の本気度をひしひしと感じた。高揚感とともに身の引き締まるような感覚を覚えたものだった。しかし、それから数カ月後、澤野の胸中を占めていたのは「焦り」だった。

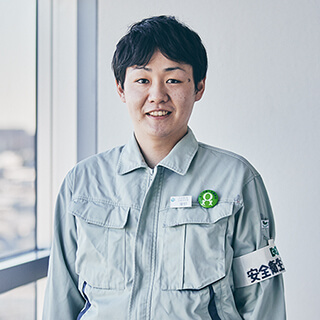
私のミッションは、設備の電気担当として電気配線をはじめ設備システムの立ち上げ、制御などを行うこと。設備設置工事の最終工程なので、建屋の工事、設備を設置する機械工事を終えてからでないと作業に取り掛かれません。しかし、前工程の工事が遅れ、私の担当段階に入った頃にはスケジュールが1カ月も押していました。
このままでは試運転に間に合わない。そうなれば生産にも遅れが生じ、顧客に迷惑をかけることになってしまう。何としても、電気工事の段階で1カ月の遅れを取り戻さなければならなかった。
澤野はまず工事内容を細かく分割して、試運転までに終えなければならない工事と、試運転と並行して作業できる工事を洗い出した。次に、試運転までに行う工事のうち、機械設置工事と並行して行える作業をピックアップ。社内の機械担当者や外部の電気工事会社などに協力してもらいながら、並行作業が可能かどうかを吟味していった。
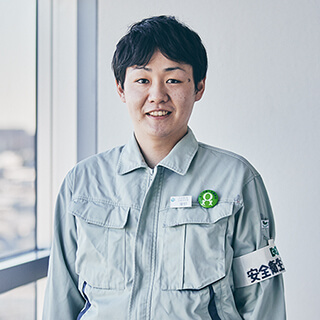
関係各所と打ち合わせを幾度となく実施し、ありとあらゆる手段を用いて工事の段取りやスケジュールを再調整した結果、何とか試運転開始までに間に合わせることができました。
工事がすべて終わったのは、2019年12月30日。試運転が始まるのは年明け。まさにギリギリだった。
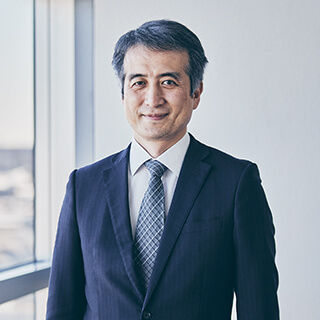
実は2019年、圧延銅箔需要が沈静化して、供給力に多少余力が出ていました。でも、工場の人たちは工事の手を一切緩めることなく、一丸となって設備増強を完遂させた。そのおかげで当社は2020年の巣ごもり需要に対応することができ、供給責任を果たせました。営業担当として、本当に感謝しています。
リードタイム短縮を目指して
サプライチェーンを
可視化する
需要の変動が激しい圧延銅箔の供給を最適化するためには、販売予測の精度を高めるだけでなく、生産に必要なリードタイムの短縮も欠かせない。JX金属の圧延銅箔は、一貫体制でつくられている。圧延銅箔の材料である銅インゴットは大分にあるグループ会社で製造され、それを倉見工場で圧延銅箔に加工。その後、茨城県の日立事業所とフィリピンのグループ会社で表面処理を施し、製品化される。この工程に必要な期間はおよそ3カ月。これでは変動する需要にタイムリーに対応することが難しかった。現状を改善するために不可欠なのが、サプライチェーンの効率化だ。この大役を任されたのが、当時入社3年目の栗原さくらである。

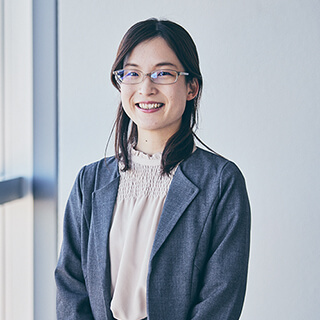
まず取り掛かったのは、納入計画の策定です。営業担当から共有された販売見通しの数字を取りまとめてエクセル上で一元化。そして週単位、日単位で計画を練り、倉見工場の生産管理部門に展開しました。
日立事業所やフィリピンのグループ会社で効率的に表面処理加工を行うためには、必要な量を、理想のタイミングで送らなければならない。そこで製品の販売見通しを一元化して、いつ、どの製品が、どのくらい必要なのかを可視化し、その計画を倉見工場と共有することで、日立事業所とフィリピンのグループ会社への供給をスムーズにするとともに、無駄をそぎ落とそうとしたのだった。
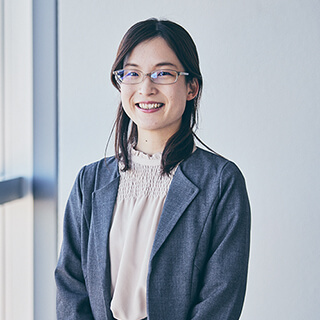
同時に、各拠点にある完成在庫や仕掛在庫の数量、運送途中の在庫数も可視化しました。どこに、どんな在庫があるのかを把握することで、急な注文にも可能な限り対応できる体制を整えていきました。
この仕組みが機能すると、3カ月のリードタイムが、2カ月ほどにまで短縮された。成果がはっきりと出たことで、2021年4月にはSCM(サプライチェーンマネジメント)担当部署が立ち上がり、銅インゴットの在庫情報や購入計画も連結されることになった。
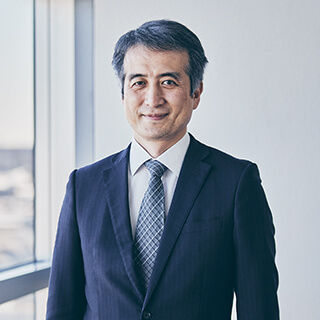
JX金属にとって、一貫製造を生かした万全の供給体制は大きな強みです。しかし、これまでは製造拠点が別々で、在庫などの情報共有もあまり進んでおらず、その強みを十分に生かしきれていませんでした。今回SCM部署が立ち上がったこと、そして現在進めているSCMシステムの導入が完了すれば、新たに増強された生産ラインや今後日立事業所に新設される工場も含めたサプライチェーンの最適化が進み、一貫製造体制の強みが色濃くなるはずです。圧延銅箔分野における当社の存在感が一層高まることになるでしょう。
JX金属の文化を
次世代へつなぐ
新規設備の導入、そしてサプライチェーンの最適化。これらが無事に完了したことで、圧延銅箔の供給能力は格段に高まり、多様な需要に応える体制が確立された。「2040年 JX金属グループ長期ビジョン」で掲げた、成長戦略のコアとなるフォーカス事業拡大への貢献度も高い。けれども、今回のプロジェクトがもたらした成果は、それだけにとどまらない。若手社員である栗原と澤野はこう振り返る。
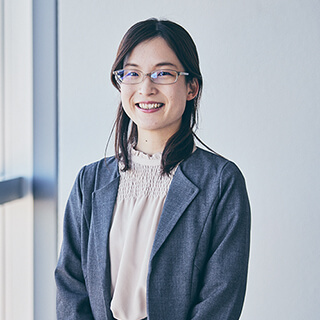
正直、大変でしたね。最初の頃は特に……。当時私は入社3年目です。そんな私が社内でも注目度の高いプロジェクトを担当するなんて夢にも思わなかった。でも、上司や先輩に協力してもらいながら試行錯誤して、何とか自分のミッションを遂げることができました。この経験で学んだのは、チームワークの大切さです。どんな仕事も一人だけではできない。だからこそ、周囲と積極的にコミュニケーションを取ることが大切。当たり前かもしれませんが、身をもってそれを感じられたことが一番の収穫だと思っています。
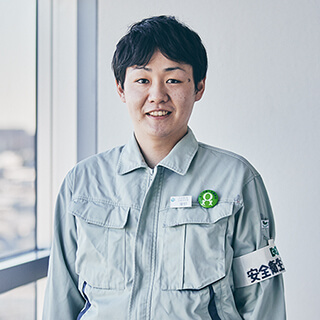
現在、群馬県館林市にあるグループ会社の工場で進行しているメッキラインの立ち上げプロジェクトでも、設計段階から試運転までを担当しています。倉見工場のプロジェクトで、不器用ながらも私なりに考え、周りの関係者を巻き込みながら完遂にこぎつけた経験が今に生きていると感じます。何より、あのときさまざまな困難を乗り越えたことで、仕事に対する自信がつきました。この自信をいつまでも持ち続け、これからも邁進していきたいです。
若手の頃から責任のある仕事を任される──。JX金属に根付いた文化を、2名の若手社員はこのプロジェクトを通して肌で感じ取り、力に変えた。これからも成功や失敗、さまざまな経験を重ねながら、まっすぐひたむきに成長していくことだろう。そして、JX金属をより良い未来へと導く主人公となるのだ。
次代を担う人材の育成。これこそ本プロジェクトの真の成果なのかもしれない。
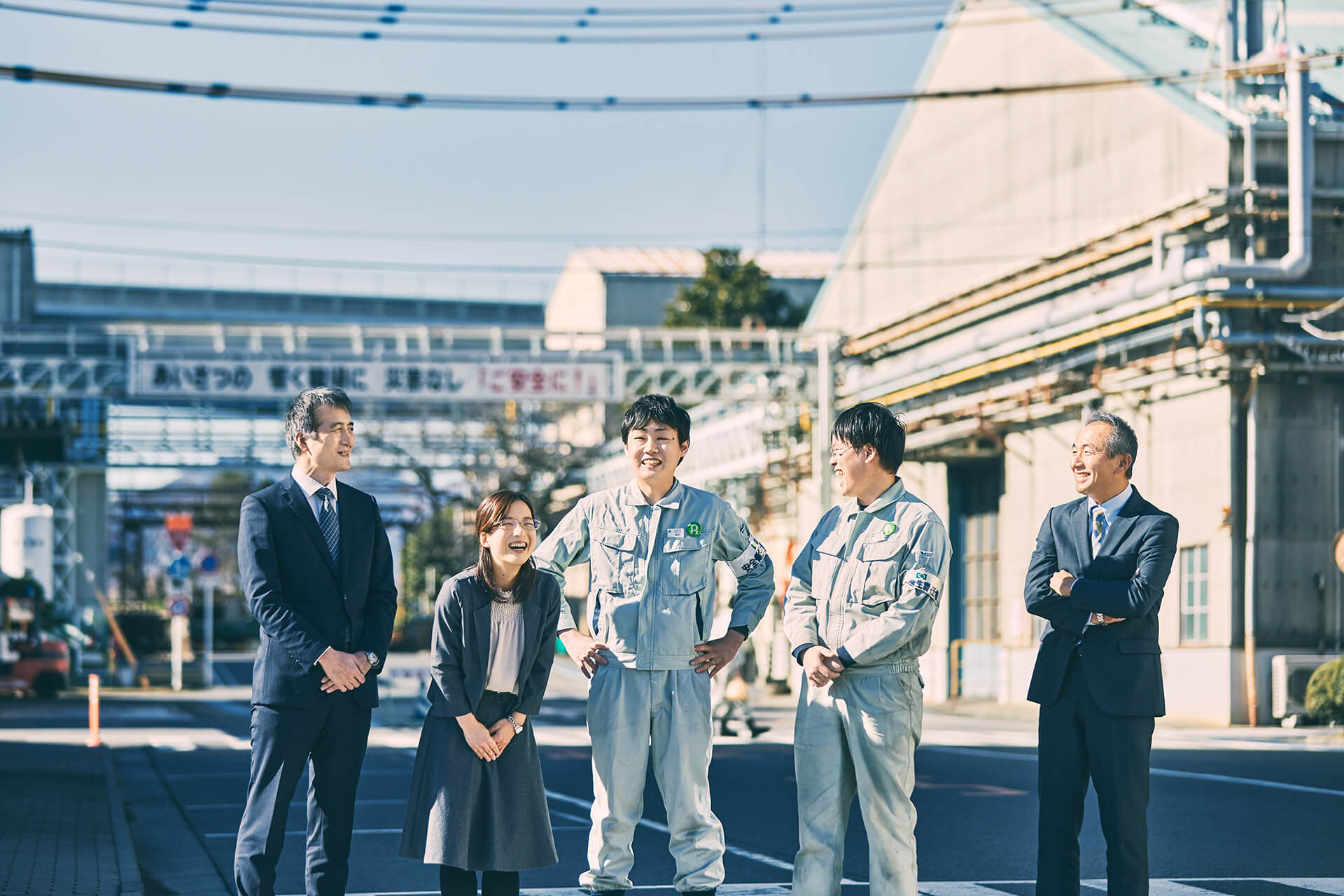